Breadcrumb
Panasonic Factory Solutions Asia Pacific Pte. Ltd.
Your partner for production equipment and automated manufacturing solutions.
Who we are
Smart Factory Solutions for any mix, any volume
Panasonic belongs to the global leading companies in the sector of the Smart Factory. Our unique DNA being a manufacturer and a total solutions provider enables us to understand the needs of our customers and to provide them with tailormade solutions for today’s challenges to be prepared for the industry of tomorrow.
Our dynamic and powerful software, managing our high-end equipment including 3rd party machines, provides our customers with a connected and responsive production environment. Any mix, any volume any time flexible to your needs with full process optimization.
Based on over 100 years of manufacturing and engineering experience, Panasonic offers trusted technology and innovation as your best partner in a connected future.
Connect to the Factory of Tomorrow
Our Solutions. Your Smart Factory
World-leading Panasonic technology matching your manufacturing needs with over 100 years of engineering experience and a wide range of factory solutions including SMT, THT, Robot & Welding, Microelectronics, UA3P equipment, and more.
Best-in-class Panasonic Software created in-house as a tailor-made dynamic solution to your manufacturing challenges: production line design, resource planning, traceability and continuous process optimization for a fully connected factory.
Trusted Panasonic Service with a strong network and trainings facilities all over the world. Providing support, machine & software trainings.
Our Divisions. For your Manufacturing
Since 1989, Panasonic Factory Solutions Asia Pacific Pte. Ltd. have been manufacturing Auto Insertion (AI) machines in-house. Over the years, Panasonic Factory Solutions Asia Pacific Pte. Ltd. have added Surface Mount Technology (SMT) machines, Laser Marking machines and Odd Form Insertion machines to their product range. With full design and advanced manufacturing capabilities for auto-insertion, our innovative solutions are versatile.
Leveraging on our lean manufacturing expertise, we continuously improve on our lead times and implement quality initiatives for optimal operation performance. We also adopt the flexi cell manufacturing system so as to enable us to achieve greater labour productivity and operational adaptability.
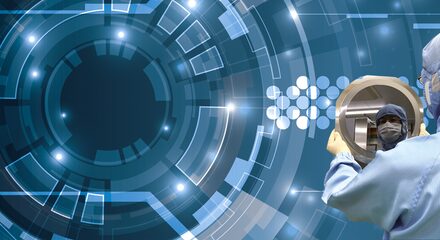
Microelectronics Solutions
With decades of experience we are continually improving our technologies.
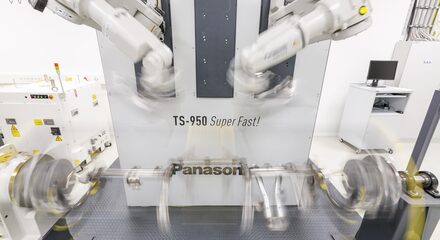
Robot & Welding System Solutions
For more than 60 years, Panasonic is developing welding technology products.
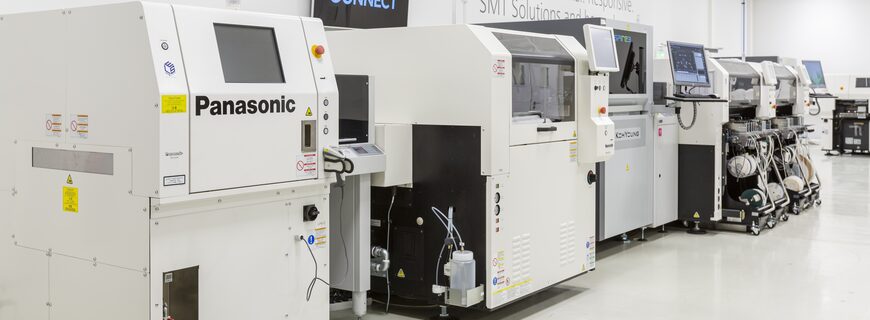
Smart Factory
In the SMT area we offer turnkey solutions for your manufacturing challenges from our portfolio of best-in-class hardware and software products for overall optimization.
Our purpose
Our Vision
Become a Core Base for Solutions and Engineering by Providing Insertion Equipment Systems Globally and Supplying Advanced Processing Processes to the APMEA Region.
通过在全球范围内提供插入设备系统并向APMEA地区提供先进的处理流程,成为解决方案和工程的核心基地。
Our Mission
To achieve total stakeholders’ satisfaction with provision of technology-driven and eco-friendly solutions.
Services we provide to our customers
Core capability
World-leading company for auto-insertion and surface mounting technology. We contribute to the productivity and connectivity of shop-floors through our advanced manufacturing capabilities and technological developments.
Research and development
Panasonic Factory Solutions Asia Pacific Pte. Ltd. engages in many Research and Development (R&D) activities to create values through cost effective design innovation that ultimately contributes to our company's growth and profitability. We also engage in joint research activities by collaborating with various Statutory Boards, Research Institutes and Institutes of higher learning to create innovative products to help businesses.
Customer Support and Solutions
Total Life Cycle Solutions
- Maximize your return on investment
- Minimize your total costs of ownership
Panasonic Factory Solutions Asia Pacific Pte. Ltd. offers solutions to prolong your equipment life cycle through maintenance and upgrades, and continuous support for productivity and quality improvement.
We specialize in Engineering and Manufacturing Automation, Robotics and IoT Solutions that enables our customers to realize Industrial 4.0 and Smart Factory Capabilities. We provide maximum customer satisfaction through our comprehensive after-sales services supported by our highly flexible sales and service staff.
PanaCIM® Enterprise Edition is a multi-level manufacturing execution system (MES) software solution for any size manufacturer. By using PanaCIM®, enterprises can add new capabilities and automate processes across their manufacturing operations.
Corporate Social Responsibility
Based on Panasonic's management philosophy, we will continue to help solve social issues and contribute to further development in order to bring about a bright new future. Click here to read more
Product Line Up SMT, THT, FATP and beyond
Printing (SMT)
SPV
The SPV Stencil Printer offers a variety of options to suit different PCBs and production processes for consistent high quality. With its high 10s/PCB cycle time, the SPV eliminates bottlenecks and ensures quality by self-cleaning after every PCB. Three conveyors and the PCB identification function provide different automatic printing set ups for a high throughput. With the machine-to-machine-communication option the SPV Screen Printer is using APC correction data to correct positional printing errors. The SPV Stencil Printer can print multiple 350x300mm (M-size) boards simultaneously. This lowers WIP inventory and reduces changeover times by processing up to 4 unique products at once. The configuration minimizes capital expenditure by reducing printer investment by 50% and maximize the floor space utilization with new hybrid board handling concept and the multi-stage board handling conveyors.
Printing (SMT)
SPV-DC
The Stencil Printer SPV-DC enables high efficiency dual lane production in a compact design. The printer is designed for high speed production without changeovers. To reduce running costs the SPV-DC is equipped with the award-winning paperless cleaning function. Solder paste can refill automatically. Solder mask and the final printing result can be verified with an internal inspection. With the machine-to-machine-communication option the SPV-DC is using correction data to correct positional printing errors. The high-speed printer SPV-DC can print on board sizes from 50 x 50mm to 350 x 300mm. With the dual lanes the printer provides a cycle time of 13s, including transfer, positioning, recognition, high-precision printing and respective cleaning. Due to the non-stop changeover, the SPV-DC allows you to prepare the next production while running the printing process.
Printing (SMT)
NPM-GP/L
The fully automated printing solution is part of the "Autonomous Factory" Concept - a factory that immediately responds to every situation and continues to evolve autonomously. Ensuring the production of non-defective items through the integrated control of autonomous uninterrupted mounting lines and floors independent of any human intervention and judgment.
Mounting (SMT)
NPM-W2
Higher productivity and quality thanks to the integration of printing, placement and inspection processes make the NPM-W2 one of the most flexible and versatile pick-and-place solutions on the market.
This machine provides the user with a tool that allows him to choose between high speed or high accuracy, depending on the PCB requirements.
In addition, the NPM-W2 is optimised for larger boards and larger components, such as PCBs up to 750 x 550 mm and components up to 150 x 25 x 30 mm (L,W,H). For high productivity, dual lanes can be used.
Features
The multifunctional NPM-W2 is equipped with a 16-nozzle head and can place 42,000 components. 120 feeders can be mounted.
Additionally, the NPM-W2 can automatically inspect solder depots and components according to the production data.
As a third function, the NPM can be fitted with the conventional HDF discharge mechanism, which ensures high-quality non-contact dispensing with a screw valve-dispenser.
Showing 4 of 17
Product Line Up Robot & Welding
TAWERS Arc welding system solution
TAWERS Software
The TAWERS “Weld Navigation” Software is a unique feature that will make your weld development much easier and faster.
TAWERS Arc welding system solution
TAWERS G4 Controller
Inheriting the evolving concept and ease of use of TAWERS.Next-generation robot controller to enhance circular business model.
Product Line Up Microelectronics
Microelectronics
PSX307A Plasma Cleaner
Building upon the PSX307 Plasma Cleaner, the PSX307A Plasma Cleaner features an enlarged plasma chamber capacity that improves productivity. In addition, the PSX307A system is able to handle full wafers (both bare and on dicing frames). Besides the increased capacity, Panasonic's original Plasma Monitoring System suppresses abnormal discharges resulting in a secure and efficient production process. Additionally, the option to include a traceability functionality ensures high level process Quality.
Microelectronics
APX300 Dry Etcher
The APX300 (option S) Dry Etcher is the perfect dry etching equipment for silicon and compound semiconductors. It incorporates a multi-wafer direct cooling system for optimal control of wafer temperature, as well as MSC-ICP (Multi-Spiral Coil type ICP) and BM-ICP (Beamed-type ICP) plasma sources to generate high density plasma. In this way, it achieves a uniform etching profile in a very short timeframe. Building upon the single wafer process chamber of the previous model (Panasonic E620), combined with enhanced process options and two different handling systems, the APX300 (option S) is extremely fast and covers a wide range of process demands.
Features and benefits of Panasonic's APX300 (option S) Dry Etcher The Panasonic APX300 (option S) Dry Etcher can process wafers such as power devices, SAW filters, communication devices, MEMS sensors and many more. The APX300 (option S) is the successor to the previous best-selling Panasonic E620 and utilizes the same single wafer process chamber. Two plasma sources are available: MSC-ICP (Multi-Spiral Coil type ICP) and BM-ICP (Beamed-type ICP). MSC-ICP is Panasonic's latest technology, developed to realize highly accurate processing. BM-ICP offers higher electron density and achieves faster processing, covering a wide range of process demands. In addition, two types of handling systems are available: Atmospheric Loading Supply and Vacuum Load Lock Supply. The Panasonic APX300 (option S) Dry Etcher is CE certified.
Microelectronics
APX300 Plasma Dicer
Plasma dicing is becoming increasingly attractive in the semiconductor market. Dies are becoming smaller and thinner and manufacturers are facing difficulties such as increasing material loss due to the width of the dicing line, mechanical damage to the dies from chipping and increasingly longer processing times due to line-by-line mechanical dicing. Panasonic’s APX300 Plasma Dicer solves these challenges and simultaneously provides a higher quality product with a lower cost of production. Features and benefits of Panasonic's APX300 Plasma DicerPlasma dicing requires a dicing street mask. After the mask is applied to the surface of the wafer and the dicing streets are exposed, the plasma process etches the exposed streets by a chemical reaction. By using a chemical etching process, a chipping-free and particle-free process is achieved. Thanks to the use of mask patterning, narrower street widths are possible – allowing more chips to be designed onto the wafer. Furthermore, the mask patterning allows complete flexibility in chip size, shape and position. The benefits of the Panasonic APX300 Plasma Dicer are: Particle-free and damage-free processHigher chip strengthYield improvementsThe Panasonic APX300 is available in a stand-alone single chamber (1 chamber) or a multi chamber (1, 2, or 3 chambers) configuration. Panasonic can provide a plasma dicing total solution to achieve a damage-free, particle-free, higher throughput and lower overall cost of production. The Panasonic APX300 is CE certified.
Microelectronics
MD-P200 Die Bonder
Unit Level Manufacturing by the synchro-motion of dispensing and bondingThe MD-P200's die bonding is carried out immediately after epoxy dispensing, thereby making it possible to finish the bonding operation before the epoxy has deteriorated. This realizes stable and high quality bonding at all bond positions on a substrate. In addition, the bonding stage camera enables pre-bonding inspection immediately after epoxy dispensing and post-bonding control immediately after the bonding of a die. This process enables manufacturing with real-time quality inspection.User-friendly operationA large touch panel and interactive software realize an easy and reliable operating environment for all users from beginners to experts.
Showing 4 of 6
Stay connected!
Enjoy all the very latest news and views from Smart Factory Solutions delivered direct to you. If you want to stay in touch with the news from Panasonic, now’s your chance. You can register to join the community – your source of all things. We are here to help! Contact us if you have an inquiry or question.
Share page
Share this link via:
Twitter
LinkedIn
Xing
Facebook
Or copy link: